- The Factories Complex of the National Company for Cement in Beni Suef, produces all types of clinker and cement of different grades. The cement production process begins within the factories complex with the stage of extracting raw materials from the quarries and transporting them using heavy equipment and dump trucks to the crusher sites, and the crushers transfer the raw materials from large blocks to crushed blocks of suitable sizes, the factory includes (6) limestone crusher at a production rate of (1200) tons / hour per crusher and (6) Clay crusher at a production rate of (400) tons / hour per crusher and (3) gypsum crusher at a rate of (350) Ton / hour per crusher and all these crushers and plant equipment are European in origin.
- After the crushing stage, the raw materials are transported to the factories complex. This is done through a network of belts. The total lengths of the internal and external belts are 22 km, with a width of (1) m, to (6) storage for limestone and clay to store (510) thousand tons and (3) storage for additives to store (30) thousand tons of sand, (30) thousand tons of iron oxide ore and (36) thousand tons of gypsum.
- This is followed by the stage of assigning the weights of mixing the raw materials according to the specified proportions according to the type of clinker that will be produced, then they are transferred to the vertical mills for grinding after mixing to obtain a homogeneous mixture of those materials at a grinding rate of (500) tons / hour for one mill. Then the dust is separated from the raw materials from through a group of filters and silos to collect dust
- After the grinding process, the homogeneous mixture is stored in (6) concrete silos with a storage capacity of (25) thousand tons per silo, the height of one silo is (71) m and diameter (25) m to ensure the continuity of feeding the primary kilns with raw materials, then the homogeneous mixture is transferred to (6) A primary furnace, each with a height of (126) m, to preheat the raw materials up to (800) degrees Celsius.
Manufacture of clinker and cement in the factories complex
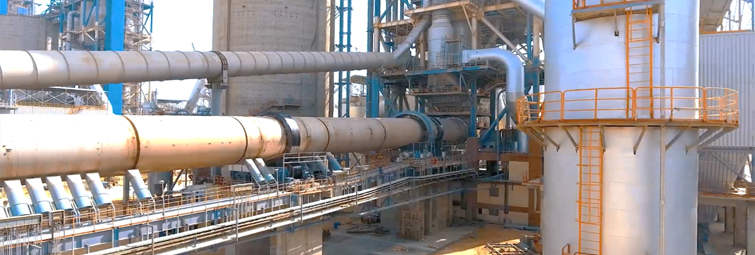
- This is followed by the stage of burning the raw materials in (6) a rotary kiln up to a temperature of (1450) degrees Celsius, which is carried out in two stages, the clinker formation stage and the first cement product. The length of one kiln is (75) m and a diameter of (5) m, with a total burning rate (6) thousand tons per day, each furnace is equipped with a backup generator with a capacity of (1) mega to ensure that the electric current is not interrupted during operation. After the calcination stage, the clinker passes through (6) coolers with a capacity of (6500) tons / day for each coolant to cool it and then store it in (12) silos, each with a height of (30) m and a diameter of (35) m of concrete with a total storage capacity of (360) thousand tons in order to ensure continuity of production and facing emergency situations.
- This is followed by the last stage of cement manufacturing, in which the clinker is ground with gypsum to prolong the setting time of cement through (6) single mills with a length of (16) m and a diameter of (6) m, and weighing up to (180) tons and at a grinding rate of (350) tons / hour per mill with a total grinding rate of (2100) tons / hour.
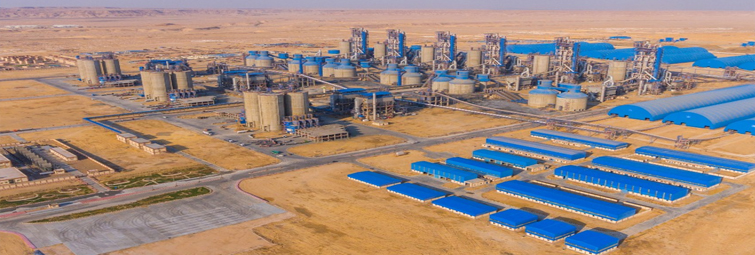
- The final product (cement) is stored in (12) silos with a total storage capacity of (240) thousand tons. The height of one silo is (64) m and the diameter is (22) m.
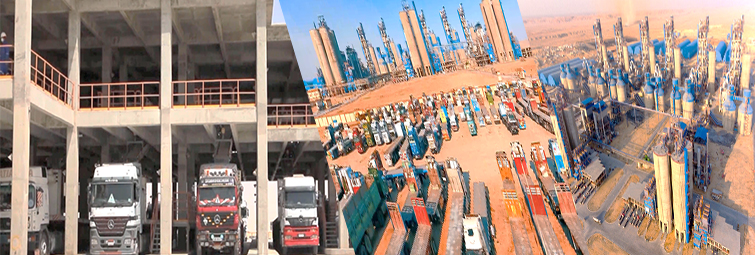
- This final product is transported to (6) cement packing buildings, where the building has been provided with (4) machines for (8) lanes for packing cement in sacks to load (4) vehicles simultaneously at a rate of 120 tons / hour per machine, and the building has also been provided With a machine for unloading bulk cement for carts, as well as packing large sacks, a package of (1) tons, attached to the packing area, a waiting area for cars ready to load bulk and packed cement, and the factory complex includes (4) weighing stations, and each station includes (2) truck scales with a load of (120) tons.
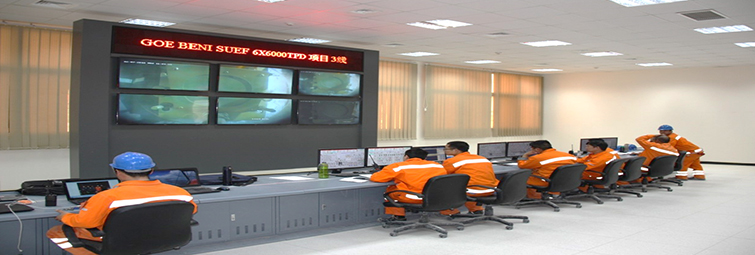
- All production stages are monitored through (3) a main control building that includes control and operating devices for the factories complex (a building for each factory consists of 2 production lines).
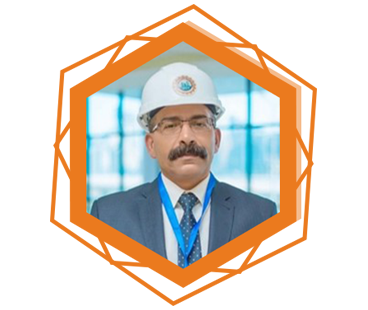